Se atribuye a Shigeo Shingo este concepto que implica algún tipo de mecanismo que ayuda a evitar (yokeru) los errores (poka). Poka-yoke es el término japonés que corresponde a mistake-proofing.
La prueba de errores consiste en añadir técnicas para prevenir los defectos y detectar los defectos tan pronto como sea posible, en caso de que se produzcan.
Poka-Yoke se utiliza a menudo como un término asinónimo, pero su significado es eliminar los defectos del producto mediante la prevención de los errores humanos (que son involuntarios). El concepto fue utilizado por primera vez por Shigeo Shingo dentro del Sistema de Producción Toyota (TPS).
Cuando un error no puede ser prevenido o detectado al 100%, la siguiente mejor opción es intentar reducir la gravedad del error y del defecto.
Objetivo:
Evitar que se produzca un defecto y cuando esto no sea posible, DETECTAR el defecto cada vez que se produzca. Existen varios niveles, esfuerzos y costes de comprobación de errores.
El equipo necesita identificar los estados óptimos y examinar la viabilidad de la implementación en los nuevos KPIV de producto o proceso.
El objetivo es en esta prioridad:
1.Prevenir los errores que conducen a los defectos
2.Detectar los defectos (no todos los errores pueden ser 100%prevenibles)
3.Reducir la gravedad del defecto
Si es práctico y necesario, tratar de implementar las tres o una combinación de las tres opciones.
A veces la tecnología no está disponible para prevenir y/o detectar los errores por lo que la siguiente mejor solución es reducir la gravedad del defecto.
Herramientas como el 5-WHY se utilizan para llegar a las causas raíz de los errores. A la hora de pensar en la prevención de errores es crucial llegar a las fuentes y a las causas raíz.
- Inspecciones
- Dos Variedades
- Tres tipos
- Conexión con el FMEA
- Examinando el Coste de los Defectos
- Ejemplos de Poka-Yoke
- ¿Cuál de los fregaderos es de menor riesgo?
- More Pictures
- Recent Articles
- t-distribution, t-test
- Six Sigma Material, Training, Courses, Calculators, Certification.
- Six Sigma Certification, Green Belt and Black Belt Certification
Inspecciones
Inspecciones:
- Sucesivas – el dispositivo/persona en el siguiente proceso comprueba y proporciona información
- Autoinspección – el dispositivo/persona inspecciona su propio trabajo
- Fuente – la persona/dispositivo inspecciona las condiciones de funcionamiento antes de realizar el trabajo
(El estado final es diseñar los errores fuera del proceso haciendo que sea imposible que ocurran)
La inspección sucesiva es una inspección de DETECCIÓNque es reactiva y proporciona información de vuelta a la fuente del error.
La autoinspección es una inspección de DETECCIÓN en la que el operario o el dispositivo comprueba el trabajo en el proceso para obtener un bucle de retroalimentación más rápido hasta el origen del error. Esto es más deseable que la inspección sucesiva.
La inspección de la fuente es la inspección más deseable ya que las otras dos ocurren más tarde en el procesoresultando en más pérdidas de tiempo y costes. El error se encuentra después de que se haya producido.Se trata de una inspección de PREVENCIÓN
Dos Variedades
Hay dos variantes de la prueba de errores
- Advertencias/Alarmas – proporciona información
- Controlar – previene y/o detiene el proceso
La inspección en sí misma no se considera una técnica viable de prueba de errores. La técnica o mecanismo que previene o detecta errores o desviaciones es el mistake proofing.
Tres tipos
Shigeo Shingo acuñó tres tipos de poka-yokes:
- Método de contacto – identifica los defectos mediante la comprobación de las características del producto.
- Método de valor fijo – un número específico de movimientos cada vez.
- Método de secuencia – determina si se siguió el procedimiento.
Los defectos encontrados en operaciones o pasos posteriores de un proceso tienen más costes asociados. Hay más materiales, mano de obra, gastos generales, producto previamente reelaborado que están en riesgo. En última instancia, si el producto llega al cliente como un defecto, los intangibles, como la reputación, pueden superar el coste tangible.
Por ejemplo, un detector de monóxido de carbono no será tan eficaz si no se conocen las entradas de los niveles peligrosos y tolerables de PPM, o si no está clara la ubicación adecuada para su instalación.
BUENO: Detecta el defecto antes de proceder al siguiente paso.
Mejor: Detecta los defectos mientras está en proceso en una operación.
Mejor: Evita que los defectos se produzcan en absoluto.
Cada proceso debe tener una prueba de errores para asegurar que los defectos no se pasen al siguiente paso y que cada operación tenga una prueba de errores para asegurar que sólo se acepten piezas sin defectos.
Conexión con el FMEA
El FMEA tiene tres categorías de:
1) Severidad
2) Detección
3) Ocurrencia
La prueba de errores se aplica para reducir las puntuaciones en Detección y Ocurrencia.
Una vez que se pruebe un dispositivo o método a prueba de errores es importante que el GB/BB haga un seguimiento con el Departamento de Calidad para actualizar el FMEA de la empresa si es aplicable.
La reducción de la gravedad también puede hacerse como otro beneficio de ahorro suave de un equipo de Seis Sigma.
Reducir todos o cualquiera de los tres valores de estas categorías reducirá el riesgo (reducir el número RPN de un modo de fallo).
El equipo Seis Sigma también actualiza su propio FMEA del proyecto y éste se convierte en el FMEA Revisado en la fase de CONTROL.
Examinando el Coste de los Defectos
Hay un coste inicial en la implementación de los poka-yokes al igual que hay un coste significativo en la implementación del SPC. Sin embargo, este coste se verá compensado con creces por la estabilidad y el rendimiento a largo plazo de la producción. En otras palabras, si se invierten los poka-yokes correctos, éstos ayudarán a reducir la variación y a desplazar la media (o la mediana) en la dirección deseada.
El gráfico siguiente muestra los costes básicos en varios niveles de DETECCIÓN.
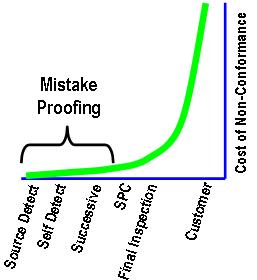
Cuanto más adelante no se detecte un defecto, mayor será el riesgo asociado. Si un cliente encuentra un defecto, hay varios costes de la mala calidad, desde el coste directo hasta una variedad de costes indirectos que pueden no percibirse inmediatamente (como las futuras retiradas o la pérdida de oportunidades de cotización).
El equipo de Six Sigma debería centrarse primero en la PREVENCIÓN. En la mayoría de los casos no se puede PREVENIR el 100% de los defectos, por lo que también es necesario invertir en la DETECCIÓN.
Ejemplos de Poka-Yoke
Los ejemplos que se enumeran a continuación son dispositivos que ayudan a prevenir o detectar errores. Sin embargo, hay diversos grados de efectividad y el equipo necesita equilibrar la obtención del poka-yoke más efectivo a la vez que es práctico y económico.
Algunas ideas para evitar errores pueden añadir tiempo al flujo de valor y añadir costes, como un proceso de inspección o un proceso de clasificación.
Más tiempo de espera equivale a más inventario, un ciclo de conversión de efectivo más largo y contradice la dirección de la fabricación ajustada.
- Corrección ortográfica en el editor de trabajo
- Códigos UPC y escáneres (reduce los errores de entrada de datos)
- Snooze
- Disyuntor
- Formación del operario
- Alarma de bajo nivel de combustible e indicador visual en el vehículor de combustible e indicador visual en el vehículo
- Instrucciones sobre el montaje de muebles o lámparas
- Funciones de guardado automático en el software
- Menús desplegables para una de datos consistente
- Inspección
- El agujero en la parte superior de un fregadero para evitar el desbordamiento
- Válvula de alivio de presión en el calentador de agua
- Cafetera apagada feature when pot is removed
- Tinting of contact lenses to assist in locating them
- L or R on the contact lens case to indicate left or right eye
- Kill switch of jet-ski attached to life jacket
- Limit switches
- «Are you sure you want to DELETE?» reminder
- Sorting of suspect material
- Force or sound detection monitors on machines
- Fire and Carbon Monoxide alarms
- Infrared imaging surveys to detect hot spots
- Kill switch on a forklift seat
- Rubble strips on shoulders of roads
- Oven Timer
- Traffic lights
- Rubble strips on road shoulders
- Various lane stripes and colors on roadways
- GFCI outlets
- Double hand jog systems
- Almost any type of sensor or alarm is a poka-yugo
- Localizador de tachuelas en la pared
- Los coches emiten un pitido si se dejan las luces encendidas
- Apagado automático de las luces del coche que se dejan encendidas accidentalmente
- ¿Qué pasaría si hubiera un sensor que reconociera el exceso de flujo y apagara las manillas?
- What if an overflow sounded an alarm or called your phone?
- What if the water amount (and even the temperature) could be programmed quickly at the faucet?
-
-
-
-
t-distribution, t-test
Mar 11, 21 10:56 AM
Exploring the t-distribution and t-test, 1 sample t-test, 2 sample t-test
-
Six Sigma Material, Training, Courses, Calculators, Certification.
Jan 29, 21 11:01 AM
One site with the most common Six Sigma material, videos, examples, calculators, courses, and certification.
-
Six Sigma Certification, Green Belt and Black Belt Certification
Jan 06, 21 08:32 AM
Describes the types of Six Sigma certification as Green Belt, Black Belt, and Master Black Belt
Más ejemplos y fotos de Mistake Proofing en www.mistakeproofing.com
También es importante evaluar si se han creado otros problemas o riesgos a partir del nuevo dispositivo poka yoke. El dispositivo no debe presentar un nuevo peligro para la seguridad, aumentar el riesgo de un modo de fallo existente o crear un nuevo modo de fallo.
Ejemplo:
Supongamos que una válvula de cierre recién instalada en la cafetera funciona para evitar el derrame por debajo en la base o en la encimera cuando se retira la cafetera.
Este es un dispositivo a prueba de errores muy agradable, pero si la bomba de agua caliente no recibe una señal de retroalimentación y continúa llenando el compartimiento del filtro, entonces esto podría desbordarse. Esencialmente, el modo de fallo de derrame se ha trasladado de un lugar a otro.
¿Cuál de los fregaderos es de menor riesgo?
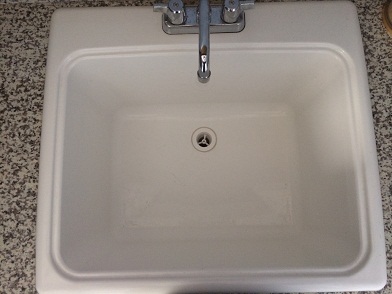
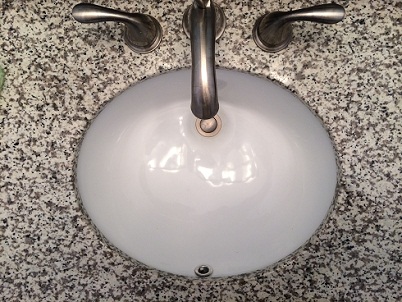
El cubo de lavandería es más profundo, por lo que podría contener más agua, pero el fregadero de la imagen de la derecha tiene un desagüe de desbordamiento como método de control de prevención de la fuente-contacto. Esto ofrece más aversión al riesgo que el fregadero de la foto de la izquierda si el agua se deja accidentalmente con el tapón puesto (¡a menos que esté tapado también!).
¿Piensa en ideas de estiramiento que mejoren aún más la prueba de errores de ambos? Manteniendo algo práctico con el coste en mente, deje que su imaginación se haga cargo.
Otras ideas:
What seemed impractical a few years ago may become practical now or in the future. What value does it add to the customer, maybe the Kano Model could draw out any interest in «delighter» features like this and understand what the customer will pay for them.
More Pictures
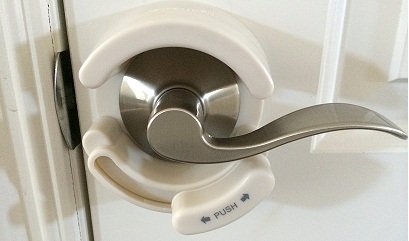
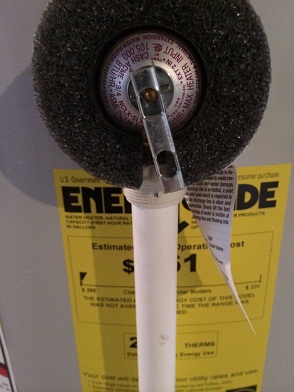
Return to LEAN MANUFACTURING
Return to the IMPROVE Phase
Search Six Sigma job openings
Subscribe to access this entire site
Templates, Statistics Tables, and Calculators