Shigeo Shingo jest przypisywany do tej koncepcji, która obejmuje pewną formę mechanizmu, który pomaga uniknąć (yokeru) błędów (poka). Poka-yoke to japoński termin odpowiadający zabezpieczeniu przed błędami.
Odporność na błędy polega na dodaniu technik zapobiegających wadom i wykrywających je tak szybko, jak to możliwe, jeśli już wystąpią.
Poka-Yoke jest często używane jako termin asynonimiczny, ale jego znaczenie polega na wyeliminowaniu wad produktu poprzez zapobieganie błędom ludzkim (które są niezamierzone). Koncepcja ta została po raz pierwszy wprowadzona do powszechnego użytku przez Shigeo Shingo w ramach Systemu Produkcyjnego Toyoty (TPS).
Gdy błędowi nie można praktycznie w 100% zapobiec lub go wykryć, następną najlepszą opcją jest próba zmniejszenia dotkliwości błędu i wady.
Cel:
Zapobiec wystąpieniu wady, a gdy nie jest to możliwe, WYKRYĆ wadę za każdym razem, gdy się pojawi. Istnieją różne poziomy, wysiłki i koszty związane z eliminowaniem błędów.
Zespół musi zidentyfikować optymalne stany i zbadać wykonalność wdrożenia w nowym produkcie lub procesie KPIV.
Celem jest w tym priorytecie:
1.Zapobieganie błędom, które prowadzą do defektów
2.Wykrywanie defektów (nie wszystkie błędy można w 100% wyeliminować)
3.Zmniejszenie dotkliwości defektu
Jeśli jest to praktyczne i konieczne, należy spróbować wdrożyć wszystkie trzy opcje lub ich kombinację.
Czasami technologia nie jest dostępna, aby zapobiec i/lub wykryć błędy, więc następnym najlepszym rozwiązaniem jest zmniejszenie dotkliwości wady.
Narzędzia takie jak 5-WHY są używane, aby dotrzeć do przyczyn źródłowych błędów. Kiedy myślimy o zabezpieczeniu przed błędami, kluczowe jest dotarcie do źródeł i pierwotnych przyczyn.
- Inspekcje
- Dwie odmiany
- Trzy rodzaje
- Połączenie z FMEA
- Badanie kosztu defektów
- Przykłady Poka-Yoke
- Który ze zlewów jest mniejszego ryzyka?
- More Pictures
- Recent Articles
- t-distribution, t-test
- Six Sigma Material, Training, Courses, Calculators, Certification.
- Six Sigma Certification, Green Belt and Black Belt Certification
Inspekcje
Inspekcje:
- Sukcesywna – urządzenie/osoba w następnym procesie sprawdza i przekazuje informację zwrotną
- Samokontrola – urządzenie/osoba sprawdza własną pracę
- Źródło – osoba/urządzenie sprawdza warunki operacyjne przed wykonaniem pracy
(Stanem ostatecznym jest zaprojektowanie błędów poza procesem, co uniemożliwia ich wystąpienie)
Sukcesywna inspekcja jest inspekcją DETEKCJI, która jest reaktywna i dostarcza informacji z powrotem do źródła błędu.
Samokontrola to inspekcja DETEKCJI, w której operator lub urządzenie sprawdza pracę w procesie w celu uzyskania szybszej pętli informacji zwrotnej do źródła błędu. Jest to bardziej pożądane niż kontrola sukcesywna.
Kontrola źródła jest najbardziej pożądaną kontrolą, ponieważ dwie pozostałe występują później w procesie, powodując więcej straconego czasu i kosztów. Błąd jest znajdowany po jego wystąpieniu. Jest to inspekcja ZAPOBIEGAWCZA
Dwie odmiany
Istnieją dwie odmiany proofingu błędów
- Ostrzeżenia/Alarmy – dostarczają informacji
- Kontrole – zapobiegają i/lub zatrzymują proces
Inspekcja sama w sobie nie jest uważana za realną technikę proofingu błędów. Technika lub mechanizm, który zapobiega lub wykrywa błędy lub odchylenia jest proofingiem błędów.
Trzy rodzaje
Shigeo Shingo ukuł trzy rodzaje poka-yokes:
- Metoda kontaktowa – identyfikuje wady poprzez badanie cech produktu.
- Metoda stałowartościowa – określona liczba ruchów za każdym razem.
- Metoda sekwencyjna – określa, czy procedura była przestrzegana.
Wady wykryte w późniejszych operacjach lub etapach procesu mają większe koszty z nimi związane. Jest więcej materiałów, pracy, kosztów ogólnych, wcześniej przerobionych produktów, które są zagrożone. Ostatecznie, jeśli produkt dociera do klienta jako wada, wartości niematerialne, takie jak reputacja, mogą przekroczyć koszty materialne.
Na przykład, detektor tlenku węgla nie będzie tak skuteczny, jeśli wejścia niebezpiecznych i tolerowanych poziomów PPM nie są znane, lub jeśli właściwe miejsce do instalacji nie jest jasne.
Dobrze: Wykrywa usterkę przed przejściem do następnego kroku.
BETTER: Wykrywa usterki podczas procesu w operacji.
BEST: Każdy proces powinien mieć zabezpieczenie przed błędami, aby zapewnić, że wady nie są przekazywane do następnego kroku i że każda operacja ma zabezpieczenie przed błędami, aby zapewnić, że akceptowane są tylko części wolne od wad.
Połączenie z FMEA
FMEA ma trzy kategorie:
1) Istotność
2) Wykrycie
3) Występowanie
Odpowiednie zabezpieczenie przed błędami stosuje się w celu zmniejszenia punktacji w zakresie wykrywania i występowania.
Gdy urządzenie lub metoda zabezpieczenia przed błędami zostanie sprawdzona, ważne jest, aby GB/BB skontaktowało się z Działem Jakości w celu zaktualizowania FMEA firmy, jeśli ma to zastosowanie.
Obniżenie śmiertelności można również przeprowadzić jako kolejną miękką korzyść oszczędnościową zespołu Six Sigma.
Obniżenie wszystkich lub którejkolwiek z trzech wartości w tych kategoriach spowoduje zmniejszenie ryzyka (zmniejszenie liczby RPN trybu awaryjnego).
Zespół Six Sigma aktualizuje również swoją własną FMEA projektu i staje się ona Zmienioną FMEA w fazie KONTROLI.
Badanie kosztu defektów
Istnieje początkowy koszt wdrożenia poka-yoke, podobnie jak znaczący koszt wdrożenia SPC. Jednakże, koszt ten będzie więcej niż zrównoważony w długoterminowej stabilności i wydajności produkcji. Innymi słowy, jeśli prawidłowe poka-yokes są inwestowane te pomogą zmniejszyć zmienność i przesunąć średnią (lub mediana) w pożądanym kierunku.
Następny wykres pokazać podstawowe koszty na różnych poziomach DETECTION.
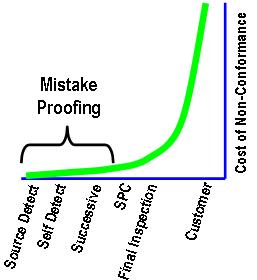
Im dalej w dół łańcucha wady idzie niewykryte, tym większe ryzyko jest związane. Jeśli klient znajdzie wadę, istnieje wiele kosztów złej jakości, od kosztów bezpośrednich po różne koszty pośrednie, które mogą nie być odczuwalne natychmiast (takie jak przyszłe wycofania lub utracone możliwości notowań).
Zespół Six Sigma powinien skupić się przede wszystkim na ZAPOBIEGANIU. W większości przypadków nie da się w 100% ZAPOBIEGAĆ defektom, więc inwestycje w WYKRYWANIE są również konieczne.
Przykłady Poka-Yoke
Przykłady wymienione poniżej są urządzeniami, które pomagają zapobiegać lub wykrywać błędy. Istnieją jednak różne stopnie skuteczności i zespół musi zrównoważyć uzyskanie najbardziej skutecznego poka-yoke przy jednoczesnym zachowaniu praktyczności i ekonomiczności.
Niektóre pomysły dotyczące zabezpieczenia przed błędami mogą dodać czas do strumienia wartości i zwiększyć koszty, takie jak proces inspekcji lub proces sortowania.
Więcej czasu realizacji równa się więcej zapasów, dłuższy cykl konwersji gotówki i jest sprzeczne z kierunkiem Lean Manufacturing.
- Sprawdzanie pisowni w edytorze pracy
- KodyUPC i skanery (redukuje błędy przy wprowadzaniu danych)
- Drzemka
- Wyłącznik automatyczny
- Szkolenie operatorów
- Alarm niskiego paliwa i wskaźnik wizualny na pojeździe
- Instrukcje montażu mebli lub opraw oświetleniowych
- Funkcje automatycznego zapisu w oprogramowaniu
- Menu rozwijane dla spójnego wprowadzanie danych
- Inspekcja
- Otwór w górnej części zlewu zapobiegający przelewaniu
- Zawór bezpieczeństwa w podgrzewaczu wody
- Czynnik wyłączający ekspres do kawy feature when pot is removed
- Tinting of contact lenses to assist in locating them
- L or R on the contact lens case to indicate left or right eye
- Kill switch of jet-ski attached to life jacket
- Limit switches
- „Are you sure you want to DELETE?” reminder
- Sorting of suspect material
- Force or sound detection monitors on machines
- Fire and Carbon Monoxide alarms
- Infrared imaging surveys to detect hot spots
- Kill switch on a forklift seat
- Rubble strips on shoulders of roads
- Oven Timer
- Traffic lights
- Rubble strips on road shoulders
- Various lane stripes and colors on roadways
- GFCI outlets
- Double hand jog systems
- Almost any type of sensor or alarm is a poka-yoke device
- Wall stud finder
- Car beeping if lights are left on
- Automatyczne wyłączanie świateł samochodowych przypadkowo pozostawionych włączonych
Więcej przykładów i zdjęć Mistake Proofing na www.mistakeproofing.com
Ważne jest również, aby ocenić, czy jakiekolwiek inne problemy lub zagrożenia zostały stworzone w postaci nowego urządzenia poka yoke. Urządzenie nie powinno stanowić nowego zagrożenia bezpieczeństwa, zwiększać ryzyka istniejącego trybu awaryjnego lub tworzyć nowy tryb awaryjny.
Przykład:
Przypuśćmy, że nowo zainstalowany zawór odcinający na ekspresie do kawy działa, aby zapobiec rozlaniu poniżej na podstawę lub blat, gdy dzbanek do kawy jest usuwany.
Jest to bardzo przyjemne urządzenie odporne na błędy, ale jeśli pompa gorącej wody nie dostaje sygnału zwrotnego i kontynuuje napełnianie przedziału filtra, to może się przelać. Zasadniczo, tryb awarii wycieku został przeniesiony z jednego miejsca do drugiego.
Który ze zlewów jest mniejszego ryzyka?
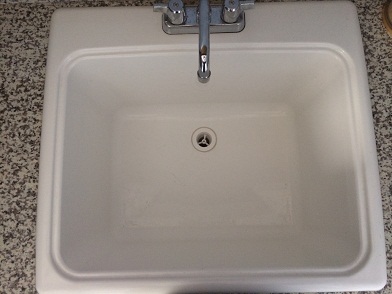
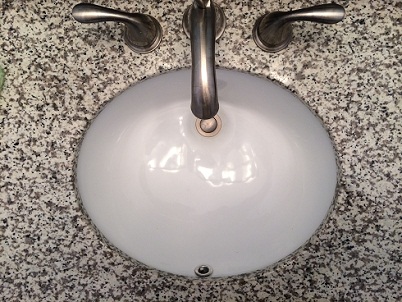
Wanna do prania jest głębsza, więc może pomieścić więcej wody, ale zlew na prawym zdjęciu ma odpływ przelewowy jako metodę kontroli kontaktu ze źródłem. To oferuje więcej ryzyko aversion niż thesink w lewym obrazku jeżeli woda jest przypadkowo opuszczać dalej z wtyczką w nim (chyba że ono jest zatykany zbyt!).
Myśl o rozciągliwych pomysłach które dalej ulepszają błąd proofing oba? Pozostając nieco praktyczne z kosztów w umyśle, niech Twoja wyobraźnia przejąć.
Inne myśli:
- Co jeśli nie było czujnik, który rozpoznał nad przepływem i odwrócił uchwyty off?
- What if an overflow sounded an alarm or called your phone?
- What if the water amount (and even the temperature) could be programmed quickly at the faucet?
What seemed impractical a few years ago may become practical now or in the future. What value does it add to the customer, maybe the Kano Model could draw out any interest in „delighter” features like this and understand what the customer will pay for them.
More Pictures
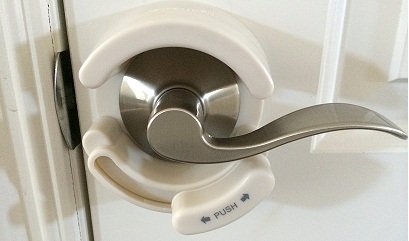
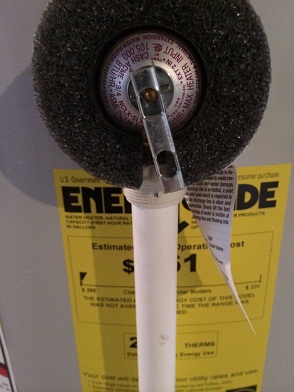
Return to LEAN MANUFACTURING
Return to the IMPROVE Phase
Search Six Sigma job openings
Subscribe to access this entire site
Templates, Statistics Tables, and Calculators
Recent Articles
-
t-distribution, t-test
Mar 11, 21 10:56 AM
Exploring the t-distribution and t-test, 1 sample t-test, 2 sample t-test
-
Six Sigma Material, Training, Courses, Calculators, Certification.
Jan 29, 21 11:01 AM
One site with the most common Six Sigma material, videos, examples, calculators, courses, and certification.
-
Six Sigma Certification, Green Belt and Black Belt Certification
Jan 06, 21 08:32 AM
Describes the types of Six Sigma certification as Green Belt, Black Belt, and Master Black Belt