Shigeo Shingo é creditado com este conceito que envolve alguma forma de mecanismo que ajuda a evitar erros (yokeru) (poka). Poka-yoke é o termo japonês correspondente à prova de erros.
Poka-Yoke é a adição de técnicas para prevenir defeitos e detectar defeitos logo que estes possam ocorrer.
Poka-Yoke é frequentemente usado como termo asinônimo, mas seu significado é paraeliminar defeitos do produto, prevenindo erros humanos (que são involuntários). O conceito foi primeiramente colocado em prática por Shigeo Shingo dentro do ToyotaProduction System (TPS).
Quando um erro não pode ser praticamente 100% prevenido ou detectado, então a próxima melhor opção é tentar reduzir a gravidade do erro e do defeito.
Objectivo:
PREVENIR a ocorrência de um defeito e quando isso não for possível, DETECTAR o defeito toda vez que ele ocorrer. Há vários níveis, esforço e custos de prova de erro.
A equipe precisa identificar os estados ideais e examinar a viabilidade da implementação no novo produto ou processo KPIV’s.
O objetivo está nesta prioridade:
1.Para prevenir os erros que levam aos defeitos
2.Para detectar defeitos (nem todos os erros podem ser 100% evitáveis)
3.Para reduzir a gravidade do defeito
Se prático e necessário, tente implementar as três ou a combinação das três opções.
Por vezes a tecnologia não está disponível para prevenir e/ou detectar os erros, então a próxima melhor solução é reduzir a gravidade do defeito.
Ferramentas como as 5-WHY são usadas para chegar às causas dos erros. Quando se pensa na imunidade a erros é crucial chegar às fontes e causas de raiz.
- Inspecções
- Duas Variedades
- Três tipos
- Ligação à FMEA
- Examinar o Custo dos Defeitos
- Exemplos de Poka-Yoke
- Qual dos lavatórios é de menor risco?
- More Pictures
- Recent Articles
- t-distribution, t-test
- Six Sigma Material, Training, Courses, Calculators, Certification.
- Six Sigma Certification, Green Belt and Black Belt Certification
Inspecções
Inspecções:
- Successiva – dispositivo/pessoa na próxima verificação do processo e fornece feedback
- Selff-Inspection – dispositivo/pessoa inspeciona o próprio trabalho
- Source – pessoa/dispositivo inspeciona as condições operacionais antes do trabalho ser realizado
(O estado final é projetar erros fora do processo tornando-os impossíveis de ocorrer)
Inspecção successiva é uma inspeção DETECTION que é reativa e fornece informações de volta para a fonte do erro.
Inspecção automática é uma inspeção DETECTION na qual o operador ou dispositivo verifica o trabalho no processo para um loop de retorno mais rápido para a fonte do erro. Isto é mais desejável do que a inspeção sucessiva.
Controle de fonte é a inspeção mais desejável, já que as outras duas ocorrem mais tarde no processo, resultando em mais tempo e custos perdidos. O erro é encontrado após a sua ocorrência. Esta é uma inspeção de PREVENÇÃO
Duas Variedades
Existem duas variações de prova de erros
- Avisos/Alarmes – fornece informações
- Controles – previne e/ou pára o processo
A inspeção em si não é considerada uma técnica viável de prova de erros. A técnica ou mecanismo que previne ou detecta erros ou desvios é a prova de erros.
Três tipos
Shigeo Shingo cunhou três tipos de poka-yokes:
- Método Contacto – identifica defeitos através do teste das características do produto.
- Valor fixo – um número específico de movimentos cada vez.
- Método de sequência – determina se o procedimento foi seguido.
Defeitos encontrados em operações ou etapas posteriores de um processo têm mais custos associados a eles. Há mais materiais, mão-de-obra, custos indiretos, produtos previamente retrabalhados que estão em risco. Em última análise, se o produto chegar ao cliente como um defeito, os intangíveis, como a reputação, podem exceder o custo tangível.
Por exemplo, um detector de monóxido de carbono não será tão eficaz se os inputs de níveis de PPM perigosos e toleráveis não forem conhecidos, ou se o local adequado para a instalação não for claro.
GOOD: Detectar defeito antes de prosseguir para o próximo passo.
BETTER: Detecta defeitos enquanto em processo numa operação.
BEST: Detecta defeitos enquanto em processo numa operação.
BEST: Detecta defeitos enquanto em processo numa operação.
BEST Evita a ocorrência de defeitos.
Cada processo deve ter a prova de erro para garantir que os defeitos não sejam passados para a etapa seguinte e que cada operação tenha a prova de erro no local para garantir que apenas as peças livres de defeitos sejam aceites.
/p>
Ligação à FMEA
A FMEA tem três categorias de:
1) Gravidade
2) Detecção
3) Ocorrência
A Prova de Erro é aplicada para reduzir as pontuações em Detecção e Ocorrência.
Quando se provar um dispositivo ou método à prova de erro é importante que o GB/BB acompanhe com o Departamento de Qualidade para actualizar a FMEA da empresa, se aplicável.
A redução de gravidade também pode ser feita como mais um benefício de economia suave de uma equipe Six Sigma.
Reduzir todos ou qualquer um dos três valores nestas categorias reduzirá o risco (reduzir o número RPN de um modo de falha).
A equipe Six Sigma também atualiza seu próprio projeto FMEA e este se torna o FMEA Revisado na fase de CONTROLE.
p>
Examinar o Custo dos Defeitos
É um custo inicial para implementar poka-yokes tal como o seu é um custo significativo para implementar o SPC. No entanto, este custo será mais do que compensado na estabilidade a longo prazo e no desempenho do produto. Em outras palavras, se os poka-yokes corretos forem investidos, estes ajudarão a reduzir a variação e deslocar a média (ou mediana) na direção desejada.
O gráfico abaixo mostra os custos básicos em vários níveis de DETECÇÃO.
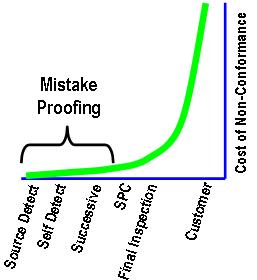
Quanto mais adiante um defeito passa despercebido, mais risco é associado. Se um cliente encontra um defeito, há vários custos de má qualidade, desde o custo direto até uma variedade de custos indiretos que podem não ser sentidos imediatamente (como recalls futuros ou oportunidades de cotação perdidas).
A equipe Six Sigma deve se concentrar primeiro na PREVENÇÃO. Na maioria dos casos, os defeitos não 100% podem ser PREVENTIDOS 100% do tempo, por isso também são necessários investimentos em DETECÇÃO.
/p>
Exemplos de Poka-Yoke
Os exemplos listados abaixo são dispositivos que ajudam a prevenir ou detectar erros. Entretanto, existem vários graus de eficácia e a equipe precisa equilibrar a obtenção do poka-yoke mais eficaz e ao mesmo tempo ser prática e econômica.
Algumas idéias para a prova de erros podem adicionar tempo ao fluxo de valor e custos como um processo de inspeção ou um processo de classificação.
Mais tempo de execução equivale a mais estoque, ciclo de conversão de dinheiro mais longo e contradiz a direção do Lean Manufacturing.
- Controle de vendas no editor de trabalho
- Códigos UPC e scanners (reduz erros de entrada de dados)
/li>>li>Snooze
>/li> - Disjuntor de circuit
/li> - Treinamento do operador
/li> - Baixo alarme de combustível e indicador visual no veículo
/li> - Instruções na montagem de móveis ou luminárias
/li> - Características de poupança automática no software
/li> - Menus puxados para baixo para uma consistência entrada de dados
/li> - Inspecção
/li> - O buraco na parte superior de uma pia para evitar o transbordo
/li> - Válvula de alívio de pressão no aquecedor de água quente
/li> - Café desligada feature when pot is removed
- Tinting of contact lenses to assist in locating them
- L or R on the contact lens case to indicate left or right eye
- Kill switch of jet-ski attached to life jacket
- Limit switches
- “Are you sure you want to DELETE?” reminder
- Sorting of suspect material
- Force or sound detection monitors on machines
- Fire and Carbon Monoxide alarms
- Infrared imaging surveys to detect hot spots
- Kill switch on a forklift seat
- Rubble strips on shoulders of roads
- Oven Timer
- Traffic lights
- Rubble strips on road shoulders
- Various lane stripes and colors on roadways
- GFCI outlets
- Double hand jog systems
- Almost any type of sensor or alarm is a poka-Dispositivo de canga
/li> - Busca de parede
/li> - Sinal sonoro do carro se as luzes forem deixadas acesas
/li> - Desligamento automático das luzes do carro acidentalmente deixadas acesas
Outros exemplos e fotos de prova de erros em www.errkeproofing.com
É também importante avaliar se foram criados outros problemas ou riscos no novo dispositivo de canga de poka. O dispositivo não deve apresentar um novo risco de segurança, aumentar o risco do modo de falha existente ou criar um novo modo de falha.
Exemplo:
Componha uma válvula de fechamento recém instalada nas funções da cafeteira para evitar derramamento abaixo na base ou bancada quando a cafeteira for removida.
Este é um dispositivo à prova de erros muito agradável, mas se a bomba de água quente não receber um sinal de retorno e continuar enchendo o compartimento do filtro, então isto pode transbordar. Essencialmente, o modo de falha de derramamento foi movido de um local para outro.
Qual dos lavatórios é de menor risco?
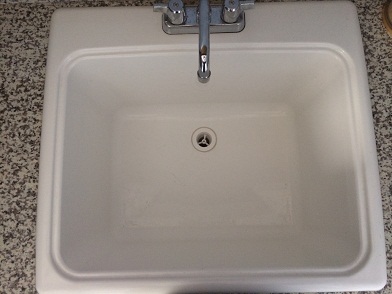
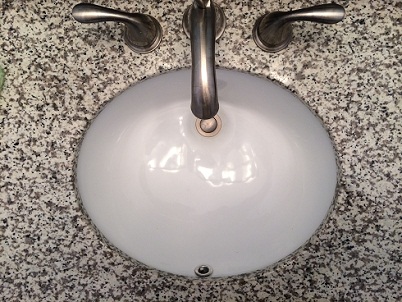
A cuba de lavagem é mais profunda para que possa conter mais água, mas o lavatório na imagem correcta tem uma descarga excessiva como método de controlo de prevenção de contacto com a fonte. Isto oferece mais aversão ao risco do que se pensa na imagem da esquerda se a água for acidentalmente deixada ligada com a ficha (a menos que também esteja ligada!).
P>Pense em ideias de esticar que melhoram ainda mais a prova de erros de ambos? Mantendo-se um pouco prático com o custo em mente, deixe sua imaginação tomar conta.
Outros pensamentos:
- E se houvesse um sensor que reconhecesse o excesso de fluxo e desligasse as alças?
- What if an overflow sounded an alarm or called your phone?
- What if the water amount (and even the temperature) could be programmed quickly at the faucet?
What seemed impractical a few years ago may become practical now or in the future. What value does it add to the customer, maybe the Kano Model could draw out any interest in “delighter” features like this and understand what the customer will pay for them.
More Pictures
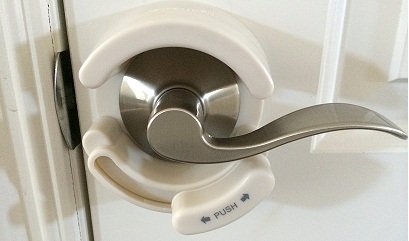
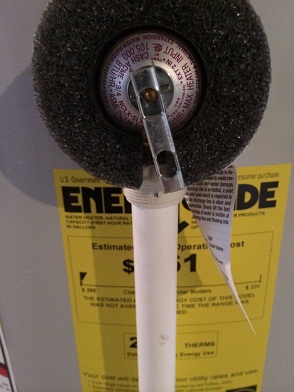
Return to LEAN MANUFACTURING
Return to the IMPROVE Phase
Search Six Sigma job openings
Subscribe to access this entire site
Templates, Statistics Tables, and Calculators
Recent Articles
-
t-distribution, t-test
Mar 11, 21 10:56 AM
Exploring the t-distribution and t-test, 1 sample t-test, 2 sample t-test
-
Six Sigma Material, Training, Courses, Calculators, Certification.
Jan 29, 21 11:01 AM
One site with the most common Six Sigma material, videos, examples, calculators, courses, and certification.
-
Six Sigma Certification, Green Belt and Black Belt Certification
Jan 06, 21 08:32 AM
Describes the types of Six Sigma certification as Green Belt, Black Belt, and Master Black Belt